Validating the hype about HIPPS
From cost-reduction and safety-enhancement to environmental responsibility, HIPPS has got all bases covered
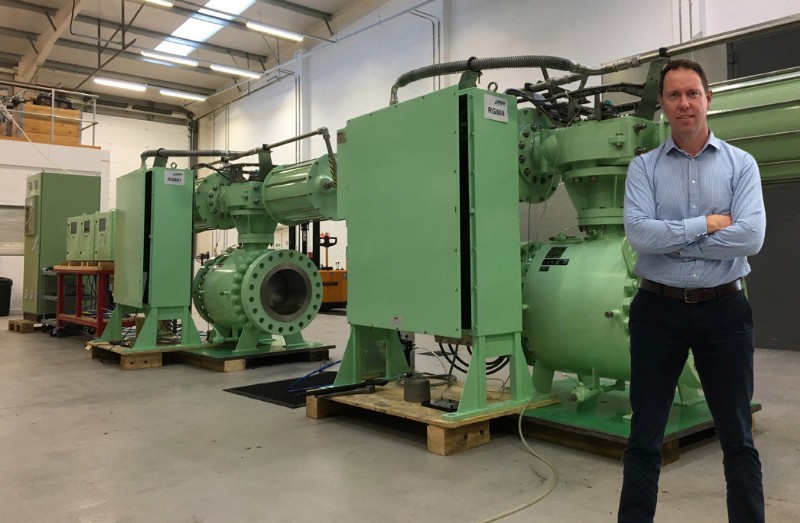
Tim Blake, Site Manager at Severn Glocon Technologies, with the FSRU
HIPPS components
A HIPPS is a complete functional loop, with three fundamental components:
1. Pressure Transmitters monitor pipeline pressure and convey a signal to the logic solver.
2. A Logic Solver captures signals from the pressure transmitters and performs a 2oo3 voting logic.
3. The Final Elements (normally two shut-off valve provide corrective action to bring the process to safe state.
Benefits
The core benefit of a HIPPS is that it activates before over pressurisation. With traditional systems, a relief valve is triggered to open during over-pressurisation: this protects the installation, but allows excess gas or fluid to escape, with potential repercussions for safety and the environment.
Furthermore, if a relief valve malfunctions, operators face heavy costs surrounding intervention and lost production. HIPPS have a high degree of redundancy to maximise reliability and reduce the risk of downtime.
HIPPS project snapshots
As a HIPPS integrator, Severn is at the forefront of developments in this technology, with several high-profile projects completed or well underway.
FSRU project
We’ve successfully completed a HIPPS installation for a floating storage and regasification unit in Korea. The objective was to protect the pipeline during the loading and unloading of gas.
Specification: max pressure 142 barg trip pressure 117 barg. Integration: 2 x 18" 900 class manual valves, Stella Controls logic solver and three pressure transmitters.
Gas export pipeline project
We’re replacing and upgrading an existing HIPPS with a larger system due to increasing demands at a top-side, land-based pipeline in Borneo. Specification: max pressure 127 barg trip pressure 76 barg. Integration: 2 x 24" 900 class valves, Stella Controls logic solver and three pressure transmitters.
The eight phases of HIPPS
Each phase of a HIPPS project is dictated by safety lifecycle standard IEC 61511, including decommissioning at end of life. Most projects involve a partnership approach, enabling operators to benefit from the specialist expertise of HIPPS integrators and other third parties.
1. Hazard and risk assessment or Hazard and operability study (HAZOP) (end-user responsibility)
2. Allocation of safety functions to protection layers (enduser responsibility)
3. Safety requirements specification (end-user responsibility)
4. Design and engineering of safety instrumented system (HIPPS integrator responsibility)
5. Installation and commissioning (HIPPS integrator responsibility) followed by validation (certifying body responsibility, e.g. TUV)
6. Operation and maintenance (end-user and HIPPS integrator, shared responsibility)
7. Modification (HIPPS integrator responsibility)
8. Decommissioning (end-user and HIPPS integrator, shared responsibility)
Tim Blake, Site Manager at Severn Glocon Technologies, says development and integration of HIPPS should draw on the combined expertise of electronic and mechanical engineers, with software engineering input if required.
“It’s important that specialist engineers interrogate the design brief and collaborate with functional safety professionals,” he explains. “This is where using an independent integrator offers a major advantage. At Severn, we employ all of these professionals inhouse. The depth and breadth of our engineering and functional safety capabilities ensures the hype about HIPPS becomes a reality.”
Tel: 0845 223 2040
Email: sales@severnglocon.com
Web: www.severnglocon.com
Telephone: | 0845 6070 710 |
Email: | sales@severnvalve.com |
Website: | www.severnvalve.com |
More information on the Severn Glocon UK Valves Ltd BVAA Member Directory Page |
Search related valve / actuator articles: Severn Glocon UK Valves LtdIssue 47Safety and StandardsHIPPS